One of the most commonly seen issues on remedial or refurbishment projects is falls, or lack of them to be more precise. Falls should always be incorporated into the roof to ensure water is efficiently directed and drained to the outlets to avoid stagnant or ponding water.
There are numerous problems associated with ponding water such as adding additional weight to the structure which may cause defections to the roof’s structural deck. It can also reduce the life expectancy of the waterproofing system. Ponding water also poses health & safety risks too, creating an environment which is perfect for Mosquito breeding and the potential for moss/algae growth which can create slip hazards.
Ponding water will most likely result in refurbishing a roof much earlier than intended or expected. One of the most common methods of rectifying insufficient falls consists of implementing a new screed to create the adequate falls.
Laying a screed to remediate insufficient falls has numerous draw backs such as
- Increased preparation processes - Including removal of the existing waterproofing membrane which also increases the risk of water ingress into the structure should inclement weather occur during the removal process.
- Increased overall project costs - Requires more material, plant & equipment for preparation and material handling plus increased labour requirements.
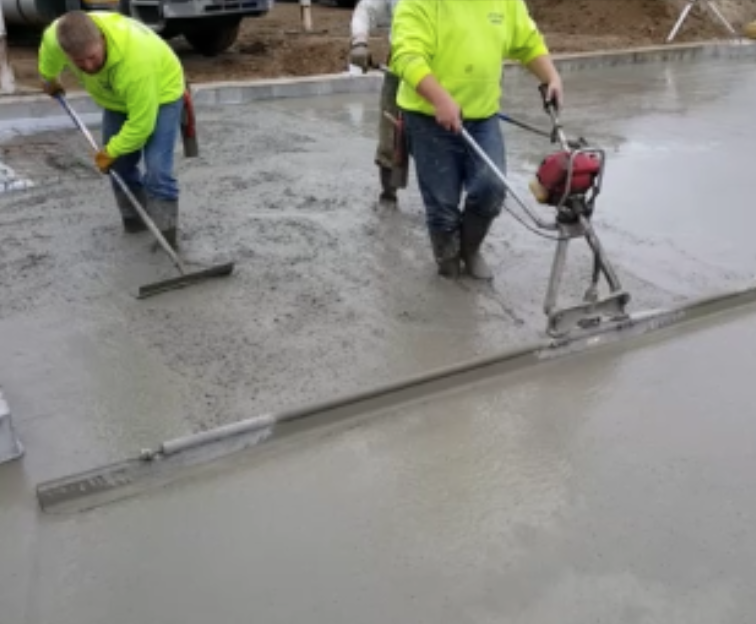
- Extended program - Due to preparation requirements, process of installation and drying times of the screed before the new waterproofing membrane can be installed. Screed to falls maybe subject to fracturing or cracking if exposed to wet weather conditions during the install and the curing process which may result in premature defects in the waterproofing membrane system.
- Human Error - Increases the risk of inaccurate or insufficient falls being created. Creating falls over large areas in various directions is almost impossible to do correctly and compliant to standards.
- Substantial increase in system weight - Anywhere from 60-120kg pm2 depending on the thickness of the screed which may exceed the structural capacity of the roof resulting in catastrophic consequences.
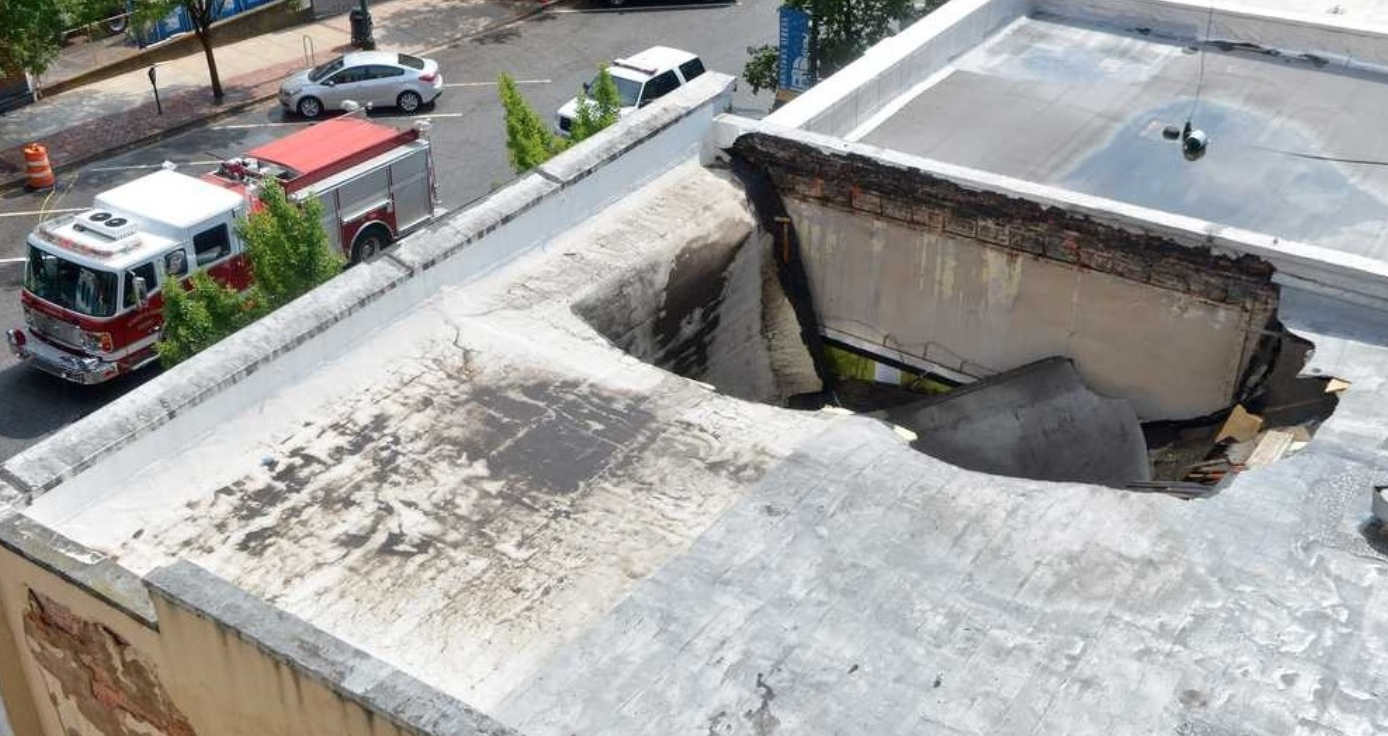
So what's the solution I hear you ask?
This is where the Fatra Tapered Insulation System comes in...
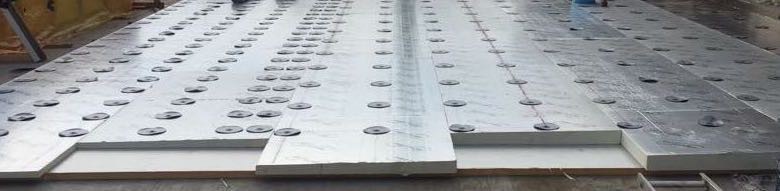
The aim of a Fatra tapered insulated roof system is to drastically reduce or eliminate ponding water when the roof structure does not or cannot provide adequate falls to prevent this from happening. By incorporating tapered insulation where insufficient falls are present, it creates and enables water to channel to the drainage outlets and reduces the risk of ponding water substantially.
Numerous surveys & studies have been carried out to assess both the cost and speed of screed to falls and tapered insulated systems. Compared to the more traditional method of rectification, Fatra tapered insulated systems offers a vast array of advantages including:
- Guaranteed accuracy of fall -As the insulation is manufactured to site specific requirements, the tapered insulated system is designed using advanced programming and software and manufactured using state of the art technology and machinery. This process creates the fall with 99% degree of accuracy providing both thermal and drainage capabilities in one single process.
- Drastically reduced overall project - As there is no need to remove the existing membrane and far less preparation required, the installation time is almost halved. In the assessment carried out by Fatra over 20 projects of various shapes, sizes and scope, the statistics show an average cost saving of 35% compared to a screed to fall system.
- Reduced risk of premature defects - The system is not affected by the vast amount of variables a screed to fall system is such as inclement weather conditions, drying times, moisture content etc so the longevity and sustained performance is maintained throughout the lifespan of the system.
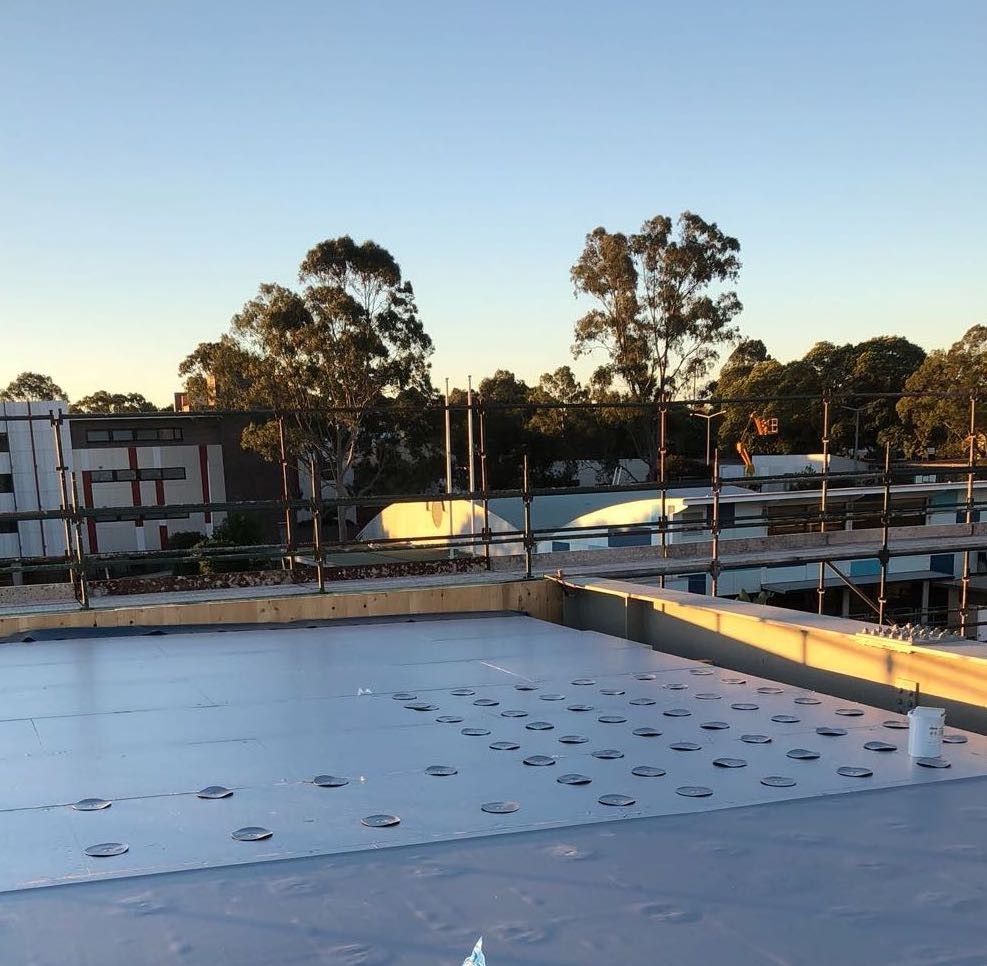
- Program Time - Not only does screed to falls take far more time to install, the drying times for a screed could be in the region of 14 days +, (depending on the product & thickness) with waterproofing installation adding further time onto the program. Compare that to the Fatra tapered insulated system where the installation of both the Fatra Waterproofing membrane and insulation can be installed at a rate of 200m2 to 300m2 per day. In the assessment carried out by Fatra, the statistics show an average decrease in the program of works of 46% compared to a screed to fall system.
- Reduced system weight - Standard sand and cement screed weighs approximately 2000kg/m3. The weight of tapered insulated systems vary from around 32kg/m3 to180kg/m3 depending on insulant type, reducing additional weight on structures considerably.
- Zero design limitations or restrictions - Fatra Tapered insulated systems are suitable for any projects, simple or more complex fall configurations. The insulation boards are designed and prefabricated to site specific requirements to accommodate even the most complex of roof shapes and drainage locations. Factory cut pre-mitred hips and valleys are available to make this process even easier and create various directions of falls. Installing a screed over large areas is almost impossible to successfully implement with correct and consistent falls. (Image below shows several design concepts and directions of fall (Right Images) and a Fatra tapered insulation design (Left Images)
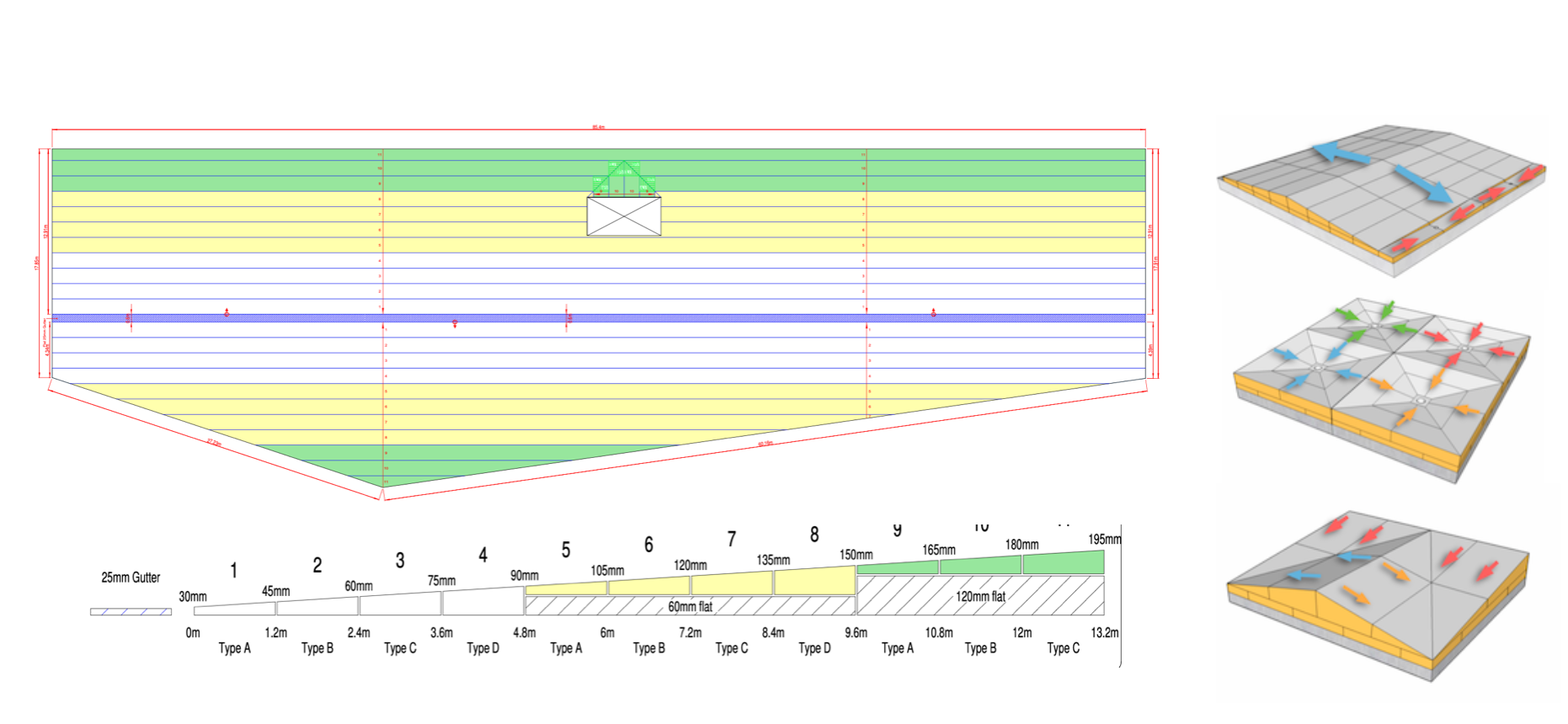
- Improves thermal performance - The Fatra tapered insulated system improves the thermal performance of the building envelope, in fact the Fatra tapered insulated system is the only system which compiles with the new NCC 2019 thermal performance criteria, all whilst offering a 30 year warranty! Typically remedial projects are carried out on older buildings that are either insufficiently insulated or more often than not, they aren’t insulated at all which means higher energy bills and extremes of both heat and cold during the summer and winter periods. Screeds provide zero thermal benefit so by implementing a fatra tapered insulated system it will lower energy costs and greatly improve the living/working conditions by regulating internal temperatures.
To find out more visit our online Project Builder or if you’d like to discuss a project contact Ashley Bowen on 0424074042 or email ashley@fatraaustralia.com.au